Technology Released: Progressing Casting Aluminum Illinois
Technology Released: Progressing Casting Aluminum Illinois
Blog Article
Development in Light Weight Aluminum Casting: Cutting-Edge Techniques for Modern Designers
What truly establishes these developments apart are the lasting aluminum alloys being developed and the high-pressure die casting techniques that are reinventing the market. Join us as we discover the leading edge of aluminum spreading technology, where technology satisfies imagination to redefine what is possible in the world of steel casting.

Advanced 3D Printing Strategies
Utilizing innovative additive manufacturing processes, progressed 3D printing strategies have revolutionized the production of intricate and personalized aluminum parts. By using high-precision printers that can work with aluminum powders or filaments, producers can develop intricate geometries and styles that were previously unattainable via traditional manufacturing techniques.
Among the crucial advantages of advanced 3D printing in light weight aluminum part production is the ability to attain light-weight yet resilient structures. This is specifically advantageous in markets such as aerospace and automobile, where weight decrease is crucial for boosting fuel efficiency and total efficiency. Furthermore, the personalization choices offered by 3D printing permit the production of one-of-a-kind and tailored parts that fulfill specific demands, resulting in enhanced functionality and performance.
Furthermore, the efficiency of the 3D printing procedure minimizes material waste and lowers the overall manufacturing time, making it a cost-efficient service for producing aluminum parts. As modern technology remains to advancement, the abilities of 3D printing in light weight aluminum production are expected to expand, using even better possibilities for innovation in numerous markets.
Computer-Aided Layout Technologies
With the innovations in innovative 3D printing methods for aluminum components, the assimilation of Computer-Aided Design (CAD) software application has actually become significantly essential in driving innovation and effectiveness in the production process. CAD developments have revolutionized the way developers and engineers produce light weight aluminum casting mold and mildews by providing exact digital modeling capacities. These software program tools enable the development of detailed styles and simulations that maximize the casting process, leading to better elements.
Among the crucial advantages of CAD in aluminum spreading is the capability to spot potential problems early in the style phase, reducing expensive mistakes and remodel during production. By simulating the spreading procedure practically, designers can evaluate elements such as cooling prices, material circulation, and architectural stability prior to a physical mold and mildew is developed. This proactive approach not just saves time and sources yet likewise guarantees that the last aluminum parts satisfy the wanted specifications.
Additionally, CAD software program makes it possible for quick models and adjustments to styles, helping with rapid prototyping and customization to fulfill certain needs. By leveraging CAD developments in aluminum casting, manufacturers can streamline their processes, enhance item high quality, and remain at the center of advancement in the sector.
High-Pressure Pass Away Casting Methods
High-pressure die spreading techniques are widely acknowledged for their efficiency and accuracy in producing intricate aluminum parts. By utilizing high stress to force molten light weight aluminum into elaborate molds at quick speeds, this technique permits for the creation of comprehensive and dimensionally accurate components. One of the vital advantages of high-pressure die casting is its capability to create components with great details and slim walls, making it suitable for applications where light-weight yet solid elements are necessary.
The process starts with the prep work of the die, which is usually made from solidified tool steel and is composed of 2 halves that create the desired component shape. The liquified aluminum is then injected right into the die tooth cavity under high stress, guaranteeing that the product loads all the elaborate functions of the mold. Once the light weight aluminum index strengthens, the die opens up, disclosing the completed component prepared for any type of essential post-processing.
High-pressure die casting is commonly made use of in various sectors, including automobile, aerospace, and electronics, where high-volume production of complex light weight aluminum parts is needed. casting aluminum illinois. Its capacity to supply tight resistances, outstanding surface area finishes, and economical production makes it a preferred selection for modern-day designers intending to introduce in aluminum spreading strategies
Lasting Light Weight Aluminum Alloys Development
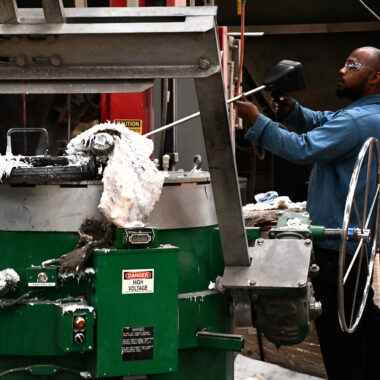
One strategy to lasting light weight aluminum alloy growth includes incorporating recycled aluminum material right into the alloy make-up. By utilizing recycled light weight aluminum, suppliers you could look here can lower energy intake and greenhouse gas emissions related to main light weight aluminum production. Furthermore, reusing light weight aluminum assists divert waste from land fills, contributing to a much more round economic situation.
Additionally, scientists are exploring new alloying elements and processing methods to improve the sustainability of light weight aluminum alloys. By maximizing alloy structures and making procedures, it is possible to boost the recyclability, longevity, and overall ecological efficiency of light weight aluminum items.

Automation and Robotics Integration
In the world of sustainable light weight aluminum alloys development, the integration of automation and robotics is transforming making procedures, leading the way for enhanced effectiveness and accuracy in production. Automation and robotics are enhancing traditional casting methods, offering various benefits to creators in the light weight aluminum industry. By integrating automation into the spreading procedure, repeated jobs that were once labor-intensive can currently be successfully taken care of by robotic systems, lowering the threat of human error and enhancing overall productivity.
Automated systems can work around the clock, guaranteeing a continual manufacturing cycle that minimizes downtime and makes best use of outcome. Robotics assimilation allows for complicated molds and complex layouts to be generated with unequaled precision, fulfilling the demands of contemporary creators for premium aluminum elements. Moreover, using automation in casting operations advertises a much safer working setting by decreasing the exposure of employees to dangerous conditions.
Conclusion
Advanced 3D printing techniques, computer-aided design advancements, high-pressure die spreading approaches, sustainable check my source aluminum alloys growth, and automation and robotics assimilation have all added to the modernization of the spreading procedure. The future of aluminum spreading is intense with constant advancement and technical improvements.
What really establishes these technologies apart are the lasting aluminum alloys being developed and the high-pressure die casting techniques that are transforming the industry. Join us as we check out the leading edge of light weight aluminum casting advancement, where innovation fulfills imagination to redefine what is possible in the world of steel spreading.
One strategy to lasting light weight aluminum alloy development includes including recycled light weight aluminum content right into the alloy make-up - casting aluminum illinois. By making use of recycled aluminum, manufacturers can lower energy consumption and greenhouse gas emissions linked with main light weight aluminum manufacturing. Advanced 3D printing methods, computer-aided style technologies, high-pressure die casting approaches, lasting light weight aluminum alloys development, and automation and robotics assimilation have all contributed to the modernization of the casting process
Report this page